Be Proactive: The Importance of Regular Wastewater Lagoon Maintenance
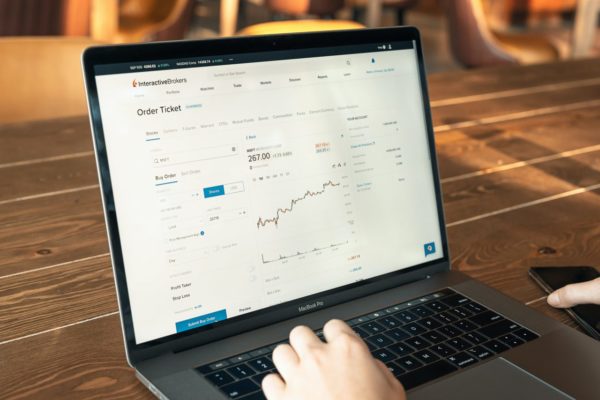
There are over 8,000 wastewater lagoons permitted to treat raw sewage in the United States. Most wastewater operators will tell you that the low operation and maintenance (O&M) cost of a lagoon is a significant advantage over a package plant or other mechanical treatment process. But it’s important to note that low O&M costs should not equate to no O&M. The key to keeping O&M costs to a minimum is to be proactive with your maintenance instead of reactive.
Lagoons tend to be more neglected than other types of wastewater treatment facilities. “Out of sight, out of mind” seems to be the common philosophy among many wastewater operators. The problem with this is that without regular inspection and proper maintenance, the lagoon will fail, and the community’s wastewater will not be adequately treated. This can lead to compliance issues when the effluent doesn’t meet the permit limits, and even public health issues if untreated wastewater flows into public streams.
One’s O&M needs will vary depending on many different aspects such as the type of lagoon, the size of the facility, how many cells the lagoon has, the type and amount of waste you are treating, and the equipment used in the treatment process. Even though it’s not required in many states, we highly recommend that an operator does a daily inspection of the facility.
Performing Daily Inspections
In the daily visit to the wastewater treatment facility, the operator should inspect the lagoon for scum, grease clumps, and other floating items that can block the pipes.
The operator should also be aware of any new or unusual odors that could indicate a problem in the treatment process, such as a malfunction of an aerator or chlorinator. Odors can also indicate an algae overload, an influx of septic water from the collection system, illegal dumping, a dead animal, or many other things that might require additional investigation/action. Plus, if your pond is near any residences, odor control must be a priority.
Other things to do during the daily inspection include:
- Inspect and clean the bar screen at the headworks
This will prevent unwanted solids from entering the lagoon from the collection system
- Check for blockages by confirming flow into the facility and between cells of the lagoon
Pipes can collapse and cause a blockage
Pipes can be blocked by animals including turtles or a build-up of solids
Inspect aerators and curtains/baffles to confirm they are anchored in place as designed - Weather can damage these devices by moving them around and interrupting power service, which interferes with their effectiveness in the treatment process
- Check the chlorine pump/feeder, including any chemicals fed in the treatment process
Check site for gas chlorine leaks
Ensure the supply of chlorine and other chemicals is sufficient
- Make sure the chlorine contact chamber is clean and free of any sludge or debris
Too much sludge can lead to sludge bulking in the chamber, causing high total suspended solids (TSS) levels and other parameter deviations
Maintaining the Landscape
Maintain the grass on the levee/dike/berm on a regular basis, depending on your location and the time of year. Cutting the grass around your lagoon regularly is extremely important to prevent the clumping that occurs when you allow grass to grow very tall before you cut it. Clumping can lead to erosion because of uneven grass coverage. The grass on that levee should look like a well-groomed lawn!
Repair any holes in the levee as quickly as possible.
Do not allow trees to grow on the levee/dike/berm. Their roots can penetrate the levee, causing costly damage. When possible, remove any tree within 50 feet of your lagoon. Trees can block natural airflow, which can affect the dissolved oxygen (DO) transfer in the lagoon, which in turn can affect the health of the bacteria in the lagoon.
Other Maintenance
Aerators and curtains/baffles should be serviced regularly as required by the manufacturer.
Last but not least, check the fence around your facility. There should be no holes in the fencing and no evidence of burrowing under the fence. Always lock the gate when you leave the site.
Taking these steps will ensure that the O&M costs of your lagoon remain low, and the facility continues to operate in top shape.